HAYS STRENGTHENED QUALITY
ASSURANCE AT COOPER-STANDARD AUTOMOTIVE
At the Cooper-Standard site in Schelklingen, Hays supported Cooper-Standard Automotive in handling issues for a major OEM working in the field of electromechanical turbocharger components.
Objective
Cooper-Standard Automotive, an automotive supplier, tasked
us with finding quality management specialists that could
assist them in supporting their customers with quality
assurance issues.
The primary focus of our activities was to address end customer issues and complaints in a professional manner. In every instance, customer satisfaction was our top priority
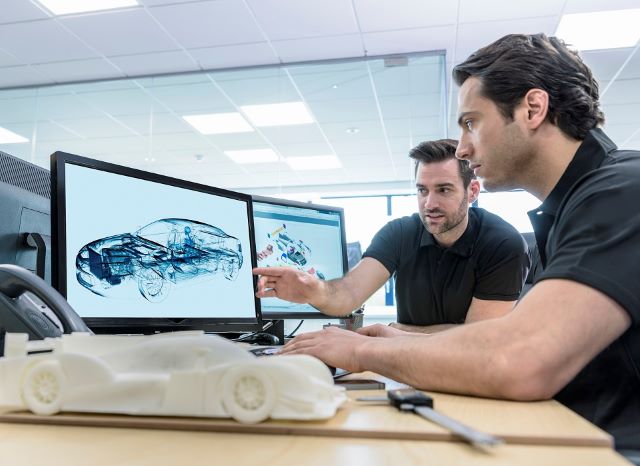
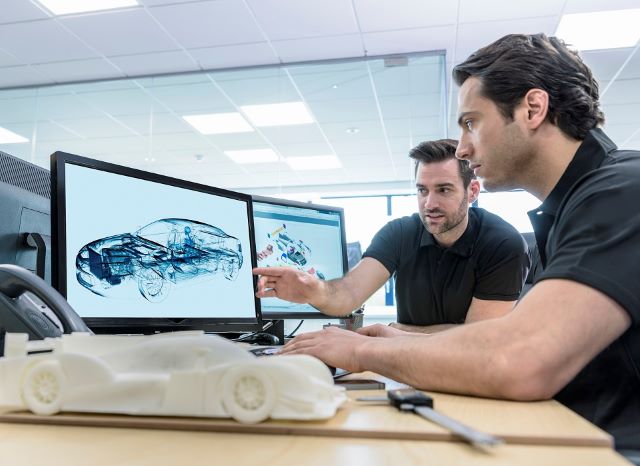
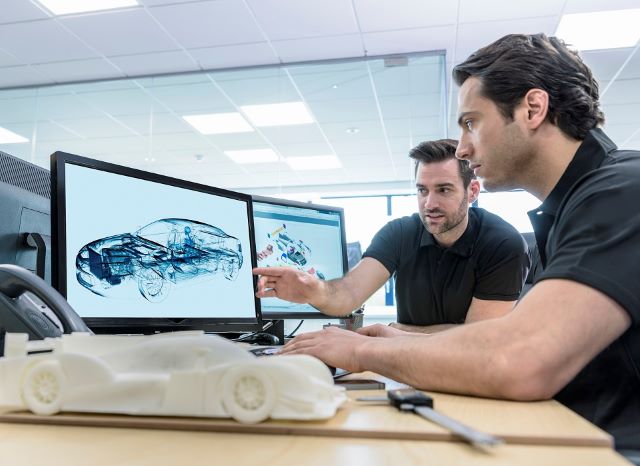
Realisation
In accordance with these requirements, we assigned an expert to the project, who, in addition to having in-depth expertise in the quality management systems ISO 9000 and QS 9001, also possessed extensive knowledge in product launches (APQP, PPAP, TS 16949). Using the PPAP (production part approval process), our expert first checked the initial sampling of the standard components. This included not only those parts which were to be delivered to the end customer, but also supplier samples. In carrying out this work, our specialist supervised and prepared the corresponding prototype test reports, carried out measurement systems analyses and coordinated the laboratory testing. He then carried out checks on the product series and produced 8D reports for processing issues.
Using these reports, he derived measures for resolving customer complaints: „When it comes to quality management, the customer always comes first. My personal goal is to ensure they receive the greatest possible satisfaction. Direct, personal contact is, therefore, the core of my work“, says our expert summing up his work at Cooper-Standard Automotive. „Different instruments are used in quality assurance, depending on the customer‘s requirements. From joint brainstorming in an international team to using scanning electron microscopy with renowned experts, we‘ve covered every facet required to get the job done.“
Highlights
At the start of the project, Cooper-Standard Automotive had sold its thermal and emissions product line. Because of this, direct responsibility for quality assurance was not always clear cut, which presented one of the biggest challenges in the project for our expert. Some of the previous machines, patents and developments had already been sold, so when it came to claiming for losses or damages it was much more difficult to get to grips with the relevant facts, conditions and responsibilities. Tensions could easily arise between the buyers and sellers in such projects, so cool heads and a large measure of perseverance were required.
Conclusion
„In retrospect, it is clear that working with Hays on this project has led to a substantial increase in customer satisfaction“, says Mr. Krznar, Human Resources Manager at Cooper-Standard Automotive.
„When we first started working together about five years ago, we requested a number of specialists using Hays. And due to the great way our projects have gone, we‘ll keep using Hays in the future.“
PDF download:

Hays strengthens quality assurance at Cooper-Standard Automotive.
You might also be interested in:

Recruitment
Trust our professional recruitment when looking for qualified staff.

Your Hays advantages
Together with us, you can simplify and accelerate your recruiting processes to fill your vacancies in no time at all.

Recruiting tips
Would you like to find out more about rehiring, successful recruitment and social media recruiting?